Properly balancing brake drums ensures uniform weight distribution, preventing noise and promoting smoother, safer braking.
Introduction
Brake drum balancing is a critical aspect of vehicle maintenance and manufacturing that directly impacts safety and performance. This is especially true for commercial vehicles like trucks and buses, where heavy loads and high speeds amplify any imbalance. A well-balanced brake drum ensures smooth rotation and braking, minimizing vibration and wear. By contrast, an out-of-balance drum can cause a cascade of issues that affect not only the longevity of the brake itself but also the overall control of the vehicle. In the following sections, we will discuss why balancing brake drums matters and explore the brake drum balancing methods.
Problems of Out-of-Balance Brake Drums
When a brake drum is not properly balanced, it doesn’t spin uniformly around its center. Even a small weight discrepancy can lead to noticeable and harmful effects. Key problems caused by an out-of-balance brake drum include:
- Excessive Vibrations: The most immediate symptom is vibration through the wheel and chassis. Drivers may feel a shudder or wobble, especially at higher speeds or during braking, as the unbalanced drum oscillates. These vibrations not only cause discomfort but can also fatigue other components over time.
- Extra Noise: The uneven rotation can create rhythmic sounds, such as humming or droning sounds when the vehicle is moving, or worsen brake noise.
- Uneven Brake Wear: An imbalanced drum distributes force unevenly on the brake shoes, causing certain areas of the drum or the brake linings to wear down faster. Over time, you may see one side of the drum or one brake shoe getting thinner, leading to reduced braking efficiency and the need for more frequent replacements.
- More Strain on Other Components: The vibration and wobble from imbalance put additional stress on suspension components, wheel bearings, and axle mounts. These parts are forced to absorb the extra motion, potentially leading to premature wear or even failure.
- Compromised Vehicle Control: Perhaps most importantly, a severely imbalanced brake drum can compromise handling. The vibrations and uneven braking force can make it harder to control the vehicle during stops, especially in emergency braking situations. In commercial vehicles, this is a serious safety hazard, as it can lead to instability or longer stopping distances.
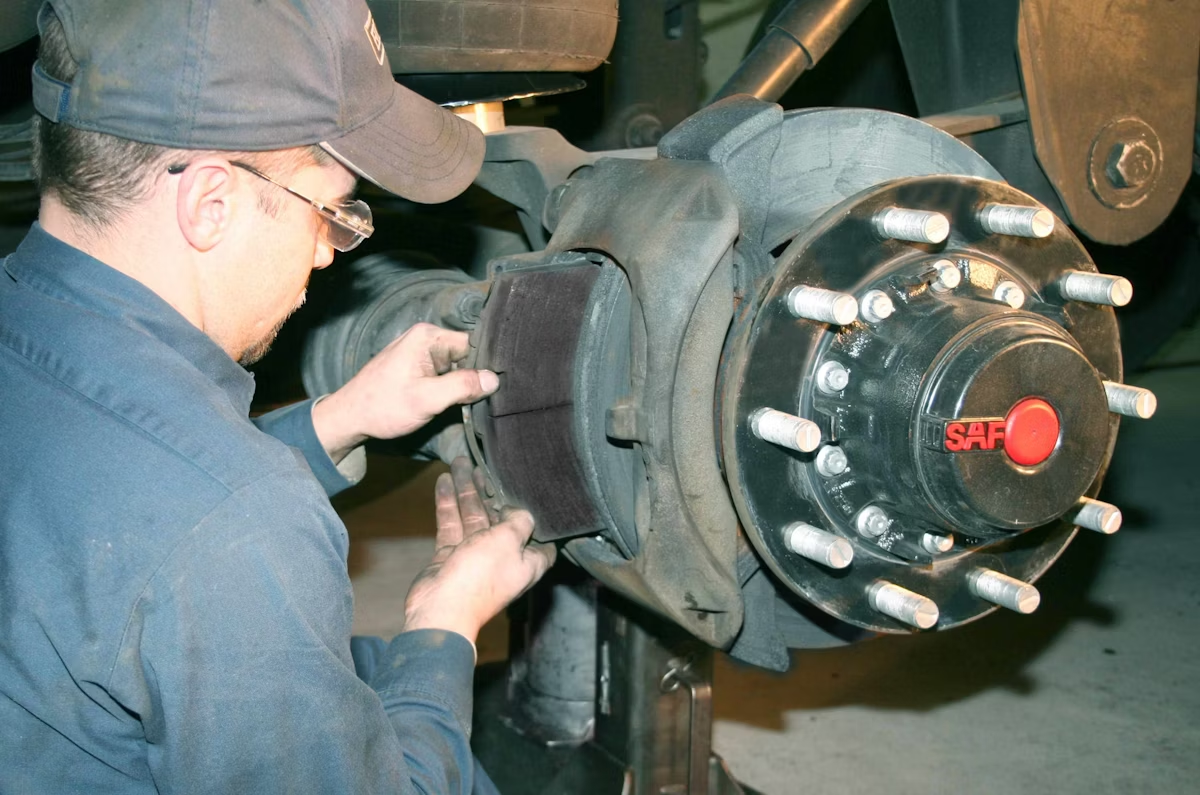
An out-of-balance brake drum is more than a minor annoyance. Ultimately, the importance of brake drum balancing lies in preventing vibration-induced problems that can compromise safety, driving enjoyment, and component longevity. It’s a step that makes a big difference in keeping heavy vehicles running smoothly and preventing avoidable repairs.
Brake Drum Balancing Methods
To eliminate the problems caused by imbalance, brake drums are balanced either at the manufacturing stage or as a corrective service. There are two main aspects to consider: the type of balancing process (static vs. dynamic) and the technique for correcting imbalance (adding weight vs. removing material). These determine how the imbalance is detected and fixed.
Imbalance Detection: Static vs. Dynamic Balancing
Balancing a brake drum is essential to eliminate vibration and ensure smooth braking performance. There are two main approaches: static balancing and dynamic balancing.
- Static Balancing: In static balancing, the brake drum is corrected for imbalance while it is stationary (not spinning). The drum is mounted on a low-friction axle or stand, and gravity causes the heaviest side to rotate downward. A weight is then added to the opposite side (or material removed from the heavy spot) to balance it. This method corrects imbalance in one plane and is suitable for slower speeds or smaller drums.
- Dynamic Balancing is more advanced. It involves spinning the drum at speed to simulate real-world conditions. Sensors detect vibration in multiple planes and identify the exact location and amount of imbalance. Dynamic balancing corrects both side-to-side and up-down wobble, making it ideal for high-speed and heavy-duty applications.
Imbalance Correction: Adding Weight vs. Removing Material
Once an imbalance is detected, it can be corrected in one of two ways:
- Adding Weight: A small steel weight is welded or bolted to the drum on the side opposite the heavy area. This method is simple and doesn’t require removing any material, making it common in light-duty or passenger vehicle drums. However, it’s less favored in commercial applications due to potential detachment under high heat and centrifugal forces.
- Removing Material: This method involves shaving off weight from the heavy side of the drum to achieve balance. It’s the preferred technique for heavy-duty drums because it provides a permanent fix that won’t shift or fall off. There are two primary removal methods: drilling and milling.
In practice, the choice of adding weight vs. removing weight, and specifically drilling vs. milling, comes down to the application and quality standards. Heavy-duty commercial brake drums (such as those on trucks and trailers) almost always favor removing material (rather than adding weights) because it provides a permanent, secure correction that can withstand continuous heavy loads.
Among removal techniques, milling is preferred for premium, high-precision applications, since it corrects imbalance with minimal impact on the drum’s structure and appearance. Drilling may still be used for simpler or cost-sensitive jobs – for instance, on economy replacement drums or where absolute precision is not paramount – but it is generally seen as a basic solution. Passenger car or lighter vehicle drums might use either method; some may simply be statically balanced with a small weight if the imbalance is minor, depending on the manufacturer’s standards and the vehicle’s performance needs.
However, most professional brake drum manufacturers (especially for commercial vehicles) employ dynamic balancing combined with material removal for the best reliability and performance. This ensures that each drum can handle the stresses of real-world operation without introducing new weaknesses.
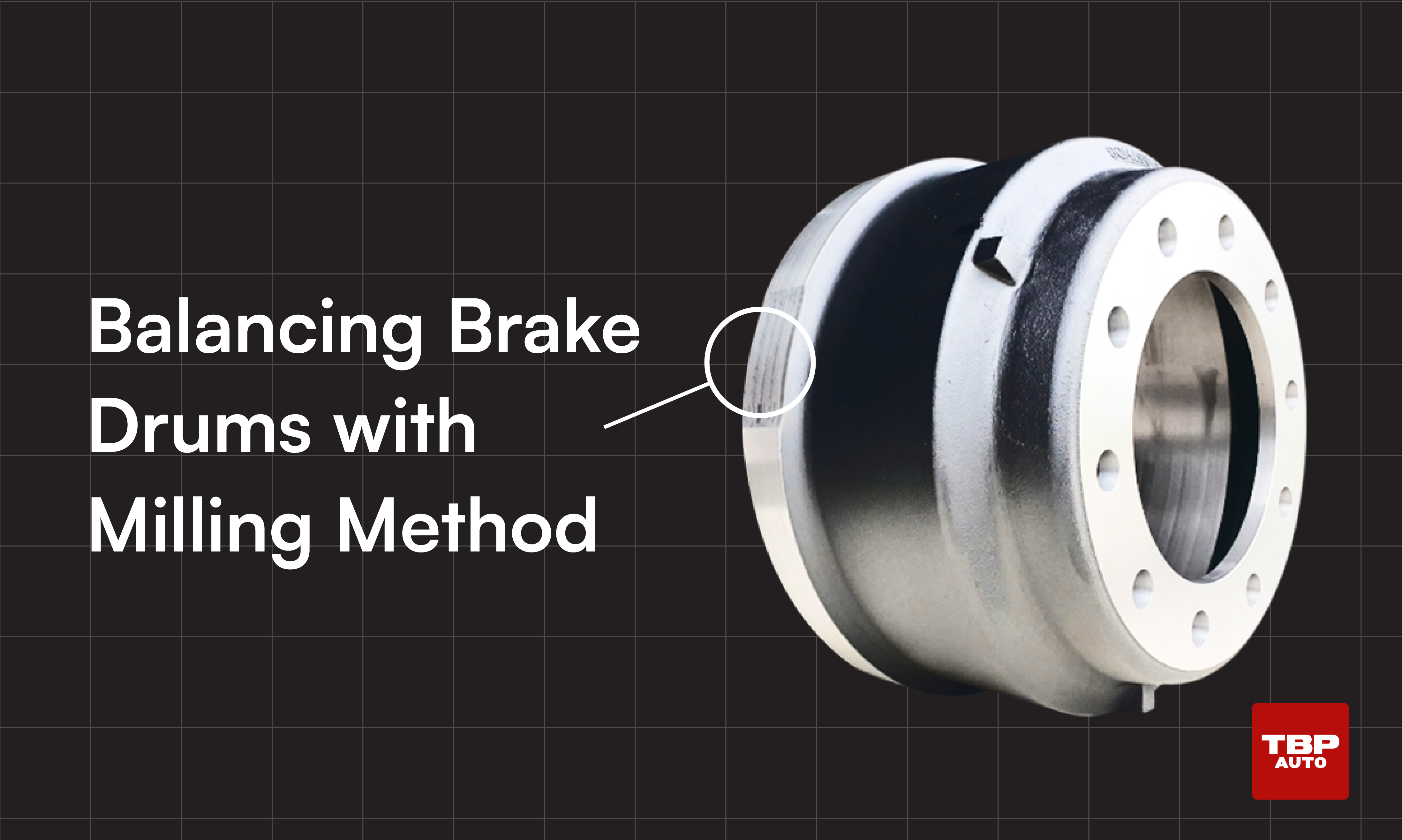
Industry Best Practice: Dynamic Balancing with Milling
Combining dynamic balancing with precise milling corrections is widely considered the industry best practice for balancing brake drums, especially for commercial vehicles. Below is a step-by-step overview of how dynamic balancing with milling is typically carried out:
Step 1: Detect the Imbalance
The brake drum is mounted on a dynamic balancing machine and spun at a controlled speed. As it rotates, sensitive sensors measure vibrations to identify any imbalance. The machine determines both the amount of excess weight and its exact location around the drum.
Step 2: Remove Material with Precision Milling
Once the imbalance is pinpointed, the machine removes material from the heavy area. Using a CNC milling cutter or integrated milling system, a shallow, smooth cut is made to reduce weight in that specific spot. The process is carefully calibrated to avoid over-removal and maintain the drum’s structural strength and symmetry.
Step 3: Verify and Test
After correction, the drum is spun again to confirm balance. The machine checks for any remaining vibration, ensuring the drum is now within acceptable tolerances. If any vibration persists, a minor secondary adjustment or investigation of other causes (such as an out-of-round drum or wheel issue) may be necessary. Only properly balanced drums should be installed on vehicles and put into use.
The dynamic-plus-milling method requires advanced equipment and expertise, but it results in brake drums that excel in real-world applications.
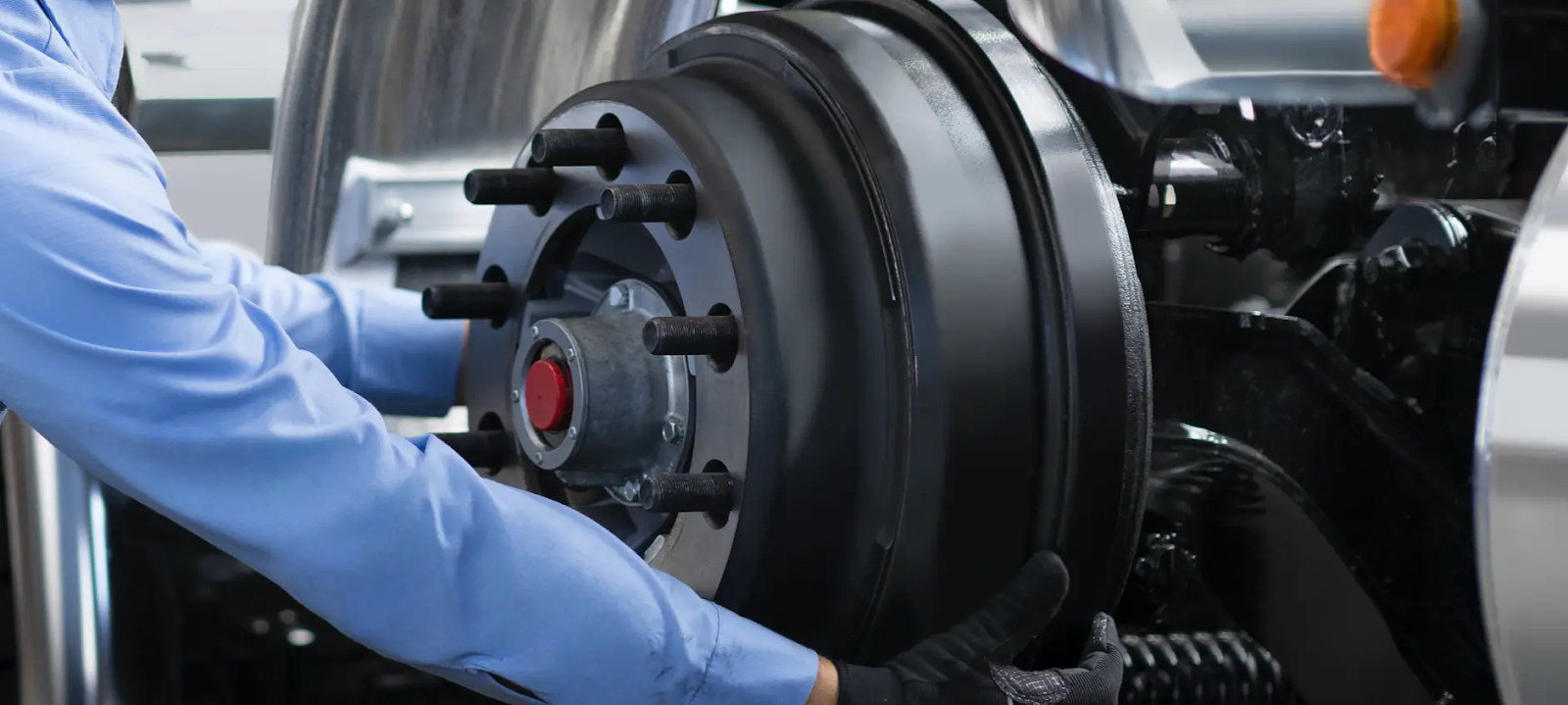
TBP Auto’s Approach
TBP Auto uses dynamic machine balancing, followed by precision milling for all of our brake drums to achieve an exceptional level of accuracy in weight distribution. Each of our brake drums is individually measured, corrected, and checked using state-of-the-art technology.
This approach offers several key benefits. First, the use of dynamic balancing ensures that the drum is balanced under conditions similar to actual use, catching even subtle imbalances that static methods might miss.
Second, milling as the corrective technique means that any material removed is done in a finely controlled way. TBP’s technicians program the milling equipment to remove exactly the right amount of material at the precise location inside the drum or on the flange, resulting in a balanced drum that meets strict tolerances.
Plus, because milling yields a smooth, blended correction, the structural integrity of the drum is preserved – there are no sudden holes or welded pieces that could introduce weak points. The aesthetic finish is also superior; TBP’s drums maintain a clean look without obvious modification marks, which is important for customers who demand not only performance but also workmanship quality.
In essence, TBP Auto’s balancing method is a premium, export-quality process. It aligns with international standards for heavy-duty brake components and caters to customers who require the highest reliability. With cutting-edge CNC milling technology, TBP Auto ensures that each brake drum is ready for the rigors of commercial service.
>>> Read more: TBP Auto’s Supreme Method of Dynamic Machine Balancing Brake Drums
Conclusion
Brake drum balancing should never be overlooked, especially in commercial vehicles where safety and durability are paramount. An imbalanced drum can lead to vibrations, noise, faster component wear, and safety risks, whereas a properly balanced drum ensures smoother rides and longer-lasting brake components. While basic static balancing or quick fixes might be enough for some light-duty situations, the gold standard for heavy-duty brake drums is dynamic balancing coupled with high-precision material removal.
At TBP Auto, brake drum balancing isn’t optional – it’s standardized for each and every one of our products. Using advanced dynamic balancing and high-precision CNC milling, we ensure each brake drum meets strict quality benchmarks. The result is a product that fleet operators can count on: consistent, durable, and ready for the road ahead. Because when it comes to commercial vehicle safety, the small details – like perfect balance – make a big difference.